Interview mit Simon Bergweiler vom DFKI
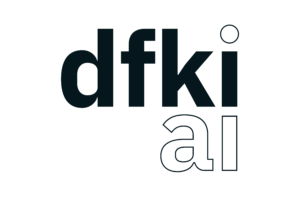
Warum arbeitet das DFKI bei T4T mit?
Wir vom Deutschen Forschungszentrum für Künstliche Intelligenz (DFKI) sind im Projekt mit drei Forschungsbereichen aus Kaiserslautern vertreten: Prof. Dr. Ing. Martin Ruskowski (Innovative Fabriksysteme), Prof. Dr.-Ing. Hans D. Schotten (Intelligente Netze), Prof. Dr. Martin, Prof. Dr. Didier Stricker (Erweiterte Realität). Wir sehen in dem Projekt die Möglichkeit, die Konzepte zu entwickeln, die zu einer zukunftssicheren und verlässlicheren Produktion im Sinne des Konzepts von Production Level 4 führen.
Welche Rolle hat das DFKI im Projekt T4T?
Das DFKI begleitet durch die Beteiligung mehrerer Forschungsbereiche mit ihren Schwerpunktthemen unterschiedliche Rollen im Projekt, alle mit dem Ziel der intelligenten Vernetzung der einzelnen Produktionszweige Montage, Qualität und Logistik. Dabei liegt der Fokus der Arbeiten auf der übergreifenden Nutzung der Daten aus heterogenen Systemen zur Steuerung, Überwachung und Optimierung von Produktions- und Unternehmensprozessen.
Welchen Nutzen erwarten Sie vom Projekt T4T für Ihr Unternehmen?
Die Forschung muss sich mit den globalen und umweltpolitischen Herausforderungen unserer Zeit beschäftigen und diese erfordern eine resiliente, wandelbare Produktion. Die Produktion muss sich auf kurzfristig verändernde Lieferketten einstellen, und die Fertigungsprozesse dynamisch anpassen können. Dabei ist es essentiell, die Technologien als Unterstützung für den Menschen durch entsprechend ausgeprägte Architekturen und Schnittstellen zu entwickeln. Das DFKI sieht enormes Potenzial in der Unterstützungsleistung des Menschen durch Methoden und Verfahren der Künstlichen Intelligenz. Ziel ist eine integrative Betrachtung von Mensch und Maschine.
Welche Nutzen können andere Unternehmen aus den Ergebnissen von T4T ziehen?
Im Projekt dient ein mehrschichtiger/multi-dimensionaler Digitaler Zwilling zur Vernetzung der Produktionszweige und der vereinfachten Nutzung von Verfahren der Künstlichen Intelligenz (KI). Aus den prototypischen Implementierungen im Rahmen des Projekts können Erkenntnisse zur abgesicherten Vernetzung von Produktionseinheiten (GaiaX), dem optimierten Tracking von Betriebsmitteln und Assets im Logistikbereich, der erweiterten Assistenz von Werkern in der Montage und der optimierten Qualitätssicherung der Montageprozesse gewonnen werden.